马上注册,结交更多好友,享用更多功能,让你轻松玩转社区。
您需要 登录 才可以下载或查看,没有账号?免费注册用户名
×
在分析产品质量问题时,往往离不开对5M1E(人员、机器设备、材料、方法、环境、测量)的六要素分析。本文通过对“变化点”因素的思考,运用变化点思维,开展对质量问题进行分析和改善。 本文选自 《质量与认证》杂志2019年4月刊
! q4 u) j/ p3 n: A M7 o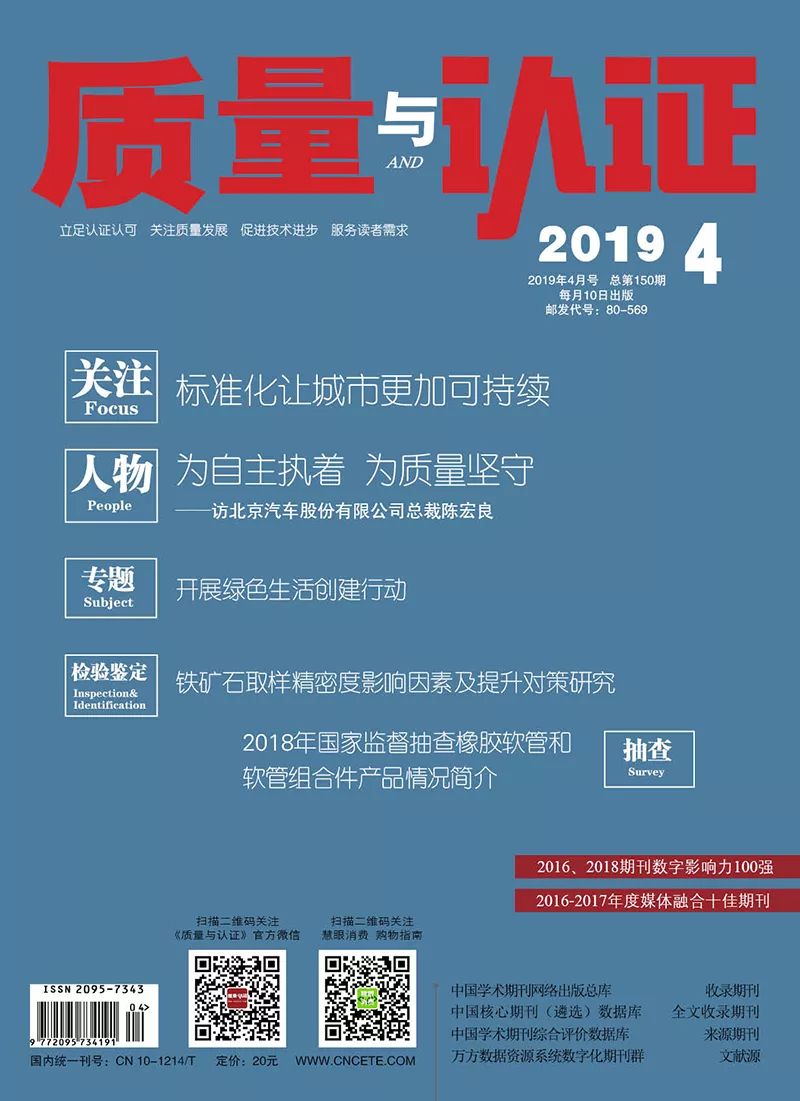 点击这里快来订阅 更多精彩,等你发现! 本文阐述的“变化点”思维目的是提醒分析者重视对各要素的变化点因素进行重点分析,因为变化点因素可能就是造成产品质量问题发生的根本原因,或者变化点因素中包含其根本原因,或者通过变化点因素能直接高效地找到根本原因。 " V u/ w* ?. l, m5 G
以下为正文: 日常的生产管理活动中,经常需要对产品的质量问题开展分析改善活动,5M1E(人、机、料、法、环、测)是不可避免的分析对象,除了要明确分析对象,还要有正确的分析思路和分析方法。有时候质量问题的分析改善像侦探破案一样,需要对5M1E进行深入分析和了解,对5M1E的分析和了解离不了质量管理的三现原则,即:现物、现状(现实)、现场,在运用三现原则过程中,一个较为重要的特征现象应被予以高度关注,那就是“变化点”因素。没有变化点,一般不会出现质量问题。通过对“变化点”因素的分析,进而改善相应的质量问题。变化点思维是提醒分析者从5M1E中的变化因素开始着手分析,变化点有时候难以被发现,有时候却显而易见,查找变化点应具有清晰的思路。从人、机、料、法、环、测等方面逐一分析研究,并从中找到变化点,而变化点往往可能就是造成产品质量问题发生的真正原因。同时,了解变化点因素也有助于我们找到真正的原因。以下通过几个事例来说明变化点思维在质量问题分析改善中的应用。 01通过变化点查找根本原因) X& D3 l$ u$ V2 @ M6 v; s) u& Q
某种产品是在6~7月开始在市场上销售,经过一个夏季的销售后,产品销售在市场上反应良好,但进入11~12月冬季销售时,在北方地区出现了一些小批量质量问题,通过调查后发现,小批量质量问题集中在北方严寒地区,而温度相对暖和的南方地区并没有出现同类质量问题,按照5M1E的变化因素看,产生质量问题的原因基本可确定是由于环境温度影响造成的。那产品为何会受到环境低温的影响而变得异常?通过进一步的取样分析和对比试验发现,组成产品的某个原材料在低温环境下其性能具有不稳定性,部分产品变得脆弱易折断,这就是最终导致产品产生质量问题的根本原因,后续通过优化配方,增加了原材料的抗低温能力,产品再没有出现过类似质量异常问题。本案例中,产品质量问题显而易见的变化点是环境温度的变化,从这个变化点找到了材料方面的缺陷原因,此缺陷就是造成该质量问题的根本原因。 02变化点本身就是根本原因
3 X: H3 O0 O2 r0 ~; O: r/ c9 N显而易见的变化点就是根本原因。某车间现场中反馈批量品质异常:某部件上带防脱锁的管件出现多个脱落,品质改善小组迅速到现场了解详情,展开了详细的三现调查(现物、现状、现场),充分对5M1E进行了咨询了解,整理出的重要线索包括以下几点。 (1)在料框中存在两种状态的防脱锁,一种松开状态,另一种自锁状态。在使用防脱锁时应人为手动到松开状态。 (2)前一个工作日有新员工刚刚在此装配工序上岗。 (3)少数故障件上可明显看出强力作业留下的印痕。 (4)新员工表示对该工序的装配作业要求不太熟悉。 (5)检查发现该工序作业指导书中的装配要求不具体。 按照变化点思维理论来看,在当日出现该异常问题之前,产线一直没有出现过此类异常情况,5M1E中唯一变化的就是新员工的上岗。在后续的排查分析中确定了新员工的不规范作业就是导致本次品质异常的根本原因,但为什么新员工会出现不规范作业的现象?进一步了解得知,班组长在现场有指导新员工作业,但培训指导新员工的时间并不长,某些极易疏忽导致出错的细节并没有明确地告知给新员工,而该工序作业指导书中也没有对装配时要听到清脆的“咔嗒”声后再进行回拉动作进行明确的表述,新员工既没有从班组长那里获得正确的装配经验,也无法从作业指导书中获取避免出错的方法,更巧合的是料框中的一些已经是自锁状态的防脱锁(不良状态)被新员工强力装配到部件上,正是这种不规范的作业方法,导致批量脱落现象的出现。在现场再次详细向新员工讲解了正确规范的装配作业方法,并对作业指导书补充了图示和详细说明,该异常问题被彻底杜绝。本案例中显而易见的变化点是新员工上岗后的不规范作业,这也是造成该品质异常的根本原因。 03变化因素中隐藏根本原因
& G5 f8 I. C% f2 z# z5 [/ ?5M1E(人,机,料,法,环,测)中物料的变化是比较难以发现的一种变化点,生产厂家或原材料供应商如果对产品进行了更改,在其不主动通知到客户的情况下,一般在客户生产现场是难以及时发现供应商产品所发生的变化的。现以物料的变化来进行浅析说明难以发现的这种变化点。 某款产品被用户投诉,用户抱怨最新批次产品在使用过程中容易出现开裂,存在有漏电的风险,生产厂家A迅速安排专业人员对故障件进行收集和分析,并对比了前几个批次的产品使用效果,确实是最新批次的产品存在开裂现象。经过分析小组对5M1E的详细分析,初步的结果是人员、机器设备、作业方法、作业环境、检测手段等都没有发生明显变化,该产品的异常有可能是由于原材料方面的原因引发的。于是分析小组对多批次的原材料进行试验发现,被投诉的批次在理化性能方面较前几个批次要差一些,联系原材料生产厂家,将开裂情况的风险向原材料厂家说明,原材料厂家坦诚告知,新提供的原材料在工艺上进行了更改,新批次的原材料因急于供货就一直没有通知生产厂家A,并且内部基于成本考虑也没有进行充分的变更试验。在原材料厂家意识到问题的严重性后,双方合力解决好了该异常问题。本案例中原材料的变更就是难以被使用厂家发现的变化点,这也是会造成产品质量异常的潜在隐患。 生产现场的作业活动是复杂多变的,在生产现场常见的问题也很多,作业方法不合理,作业流程不顺畅,设备故障,安全事故,产品批量不合格,产品标识混乱等。当问题发生后,有时候相关权责人员并没有真正仔细地分析问题,通常解决方式是采取补救行动,而不是针对发生问题的根部原因采取纠正措施,在分析问题时,也没有彻底去寻找问题的来源,不清楚问题点的核心所在,而实际上分析和解决问题过程中需要遵守的方法是:了解现状(充分掌握事实情况),查明原因,采取对策,效果确认,予以标准化。在这个分析改善过程中应重点关注5M1E中的变化因素。有时候变化因素可能就是真正的原因或者它能有助于帮助找到真正的原因,只有解决了真正的原因才算是彻底的解决了问题。 ) W8 v, y7 C/ k# @: K; x4 T' I
|