. \% u( @, i4 X [5 r3 v* m3 u/ W( E8 q/ r, }5 O
一位在质量管理领域从业20年的同仁,分享自己对5why分析法的优化和改良。
2 d# |3 k0 o6 F) o
四个层面的原因分析
% U/ h- g) K' q# R. L/ }% w2 E在出现质量问题的时候,很多企业强调多问几个为什么,以找到问题的根本原因,深层次原因。这无疑是比简单地寻求表面解要好得多。但看过很多企业的工程师所写的问题分析和改进报告,我最大的感触是大家不知道5why要问到什么时候,是不是一定要问5个呢?问4个行不行呢?问6个,问10个行不行呢?每个why应该找出几个原因呢?5个why是串联关系层层递进的?还是可以呈树形关系呢?别告诉我你没有过这样的疑问,如果没有过疑问,那只能说明你没有很好地用过5why。
针对产品质量问题的原因分析,我提出了四个层面的原因分析的理论。用来明确原因分析应该覆盖哪些方面,应该深入到什么深度。
这四个层面分别为:
" U8 [" r7 T7 {产品层面;
过程层面;
控制方法层面;
管理层面。
7 J# o# @) \+ C6 S
9 c( t, P9 U6 |! q
理论依据
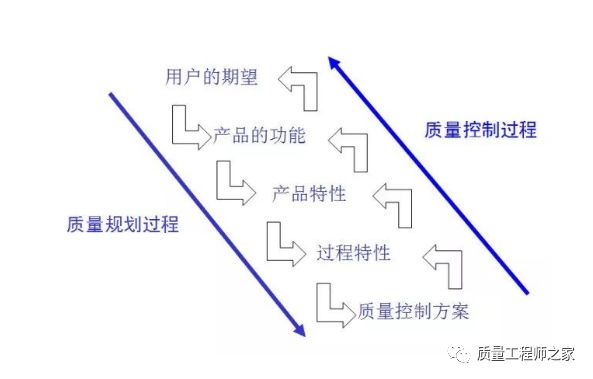
怎么来理解这四个层面呢?《什么是质量?》一文中所给出的质量实现过程的用户期望的四步翻译转换的模型在这里就可以帮助我们了。
8 ]4 A5 ~ {0 A+ V/ ?5 J; S& }' i产品层面的原因分析
& y5 ~3 Y2 g7 q; {5 P0 C客户的期望,是由产品的功能来满足的。面向产品的最终用户的功能,是由产品的下级系统的功能、子系统的功能来满足的。层层向下,作为最底层的功能组件的功能,是由各个零部件的产品特性,例如长度、距离、位置、硬度、粗糙度、圆度、材料疲劳强度、电阻、电压、焊接强度,等等,具体的产品特性来实现的。
最终产品所要求的功能、上级系统所要求的功能,如果不能被可靠地实现、如果不能满足功能在量化程度上的要求,这类质量问题我们明确为功能适用性问题。功能适用性问题,我们也称为功能障碍问题。它一方面的表现是我们所期望的功能不能实现,或者不能满足要求,另一方面的表现是客户不期望的功能的出现。例如噪音、异响、断裂、漏油等等,都是功能障碍问题。
! M7 J2 S/ M- L# h而可能引起功能障碍的产品特性的不符合,是符合性问题。例如粗糙度超差,可能会引起异常磨损。异常磨损是功能障碍,而粗糙度超差是符合性问题。
) q% }; j o! d+ C5 E
如果产品功能要求是函数Y,保证功能的相关产品特性就是自变量X。可以有函数关系式y=f(x1,x2,x3,x4...)。大写的X、Y代表多个变量组成的向量,或者变量组。小写的x,y代表具体的单个变量。从产品的功能障碍出发,即y不符合要求。找到是哪个相关的产品特性x所带来的影响,这个层面的原因分析,就叫做质量问题的产品层面的原因分析。
例如某个零件的密封螺纹处漏水,漏水是密封性功能要求出现障碍。其产品层面的原因是密封螺纹孔和螺柱的压型不匹配。再例如缸体的油道泄露,泄露是功能障碍,其产品层面的原因是铸造油道孔壁有疏松。再例如某发动机异响,其产品层面的原因是凸轮轴基圆上有加工振纹,导致滚子摇臂在运行时产生振动。
因而说产品层面的原因分析,要从产品的功能障碍出发,具体到具体零部件上的具体产品特性。有可能是某产品特性设计选择不好,也有可能是该产品特性加工制造时不符合图纸要求。
* ~# [( |; |6 W/ L过程层面的原因分析
$ @* t% `0 @5 i2 X+ A$ Y% ?8 A针对产品特性在加工制造时不符合要求,也即符合性问题,我们就需要进入第二个层面的原因分析,过程层面的原因分析。如果是生产制造过程的产品检测环节发现了某产品特性不满足要求的问题,那就直接是符合性问题了,也就可以直接进入过程层面的原因分析了。
9 q g7 g1 L6 c! E7 ?
概括地说,过程层面的原因分析,是需要从产品特性的不符合出发,寻找到具体的生产线、具体的工序、工位、工步的具体的过程特性的原因。这个时候生产加工过程结果,也就是产品特性,就可以当做函数Y了。而过程的输入——过程特性,和和影响本工序加工结果的上游工序所产生的产品特性,作为自变量X。那么过程层面的原因分析就又是个由某个y的不符合,寻找相关的x及合适的x的取值范围的过程了。
例如图纸要求的密封螺纹牙形被错误地加工成为紧固螺纹牙形,其过程层面的原因是孔的螺纹加工刀具型号使用错误;产品产生铸造疏松是因为产品的机构上存在热结,而热结作为最后冷却的部分,而且没有铝水的补充通道,造成最后凝结部分冷却收缩后疏松;凸轮轴加工振纹是因为精磨工位砂轮动平衡不好,而且砂轮主轴间隙过大,导致砂轮在加工过程中振动。
过程层面的原因,可能是工艺设计选择没有设计好;也可能是工艺设计没问题,而过程特性没有控制好而不符合工艺要求了。
2 z( v" x) @ H8 M" P6 N控制方法层面的原因分析
6 s0 f: n3 N7 |' m% ]过程层面的原因找到了,接下来就要考虑控制方法层面的原因。
所谓控制方法是我们在现场质量控制过程中为保证产品质量所采取的方方面面的所有活动。主要包括两个方面:一是对过程各项输入——人、机、料、法、环境、物流等各个方面技术特性的管控方法,以保证过程输入的稳定;以及对过程输出,也即产品特性的检测方法,以便在过程输出发生波动时及时调整过程的输入。
因而控制方法层面的原因要考虑两个方面,对过程输入的管控,和对过程输出的检测和监控。
( i, s* \6 q7 m$ L# _1 f; ~
例如螺纹牙形加工错误问题,对螺纹孔加工刀具的型号在换刀图中没有明确的规定,换刀作业指导书中没有要求核对刀具型号;对产品螺纹形状没有明确的检测要求;对螺纹止通规牙形的选择也没有明确,止通规选择错误。再例如产品铸造疏松,对模具热结处没有强制冷却要求,没有产品审核解剖检验工件内部的疏松;再例如凸轮轴振纹问题,对砂轮的动平衡没有明确的规定,在砂轮修模时没要求检测动平衡;对砂轮主轴的间隙、跳动没有在设备预防性预见性维护保养中规定定期检测;对凸轮轴有粗糙度检测,但没有波纹度检测和振纹检测(沿着圆周方向)。
; c" G& V% X" n% m* D1 ^7 L. L
管理层面的原因分析
; k- q6 g: ^# F7 b) K0 z: D2 T8 r. w管理层面的原因分析,在上图中就找不到相关的转换关系了。如果上图中的四步翻译转换是下层基础,那么管理层面的原因分析就是要找到保证这些基础的上层建筑方面的原因了。
管理层面的原因,就是要找到于前三个层面的原因相关的:
; @& C) P1 O) w, Z N
例如螺纹密封问题,由于产品设计人员不了解紧固螺纹和密封螺纹的差别,产品设计人员的经验和能力不足;企业未建立起典型密封结构的设计指南。产品缩孔问题,企业在项目阶段未开展产品设计的工艺性分析,未能识别出热结的影响;铸造过程设计和模具开发阶段未使用模流分析等模拟计算验证手段来分析识别铸造冷却过程中的疏松等风险。凸轮轴振纹问题,产品设计人员经验不足,未识别出对凸轮轴振纹的要求;工艺设计人员开展PFMEA分析过程中未能识别高速旋转件(砂轮)的动平衡要求;未能识别出磨床主轴跳动和主轴间隙的要求,工艺设计人员能力不足;PFMEA采用头脑风暴法和经验积累方法,未使用功能树分析和质量功能展开来支持PFMEA,方法不够好,需要提高。
9 |8 C$ w+ v! c5 T; t. n; i
四层分析法的优点
9 `; P- j8 |* I: s- p4 k* `5 ]由以上结合实际案例的讲述,大家可以看出,这里所说的四个层面的分析,就是把5why的方法具体化套路化了。而且比5why更明确,更细化。利用原因分析的四个层面的指导思想,就更容易帮助普通工程师在质量分析中做到深入分析系统性原因了。
8 _! R; K9 E( m
一个点上的产品质量问题,如果按照四个层面的原因分析的方法,就可以找到某些管理方面的问题。在线上甚至面上做改进,就可以避免以后一系列的相似的问题,就可以逐步把企业的整体质量体系建设逐步完善起来了。所以我在工作中更喜欢强调四个层面的原因分析,而不太喜欢讲5why。) w( S8 `# h) `4 l( W1 Y2 G" p1 H, y7 I
2 B/ ` b4 ]( s
殊途同归
Y. w6 a; t" V
因为我看到不同的企业同样的质量工具在实践应用时会存在很多的差异。德系企业、美系企业、日系企业的质量体系要求在总体上其实是相通的,大的思路是一样的。但在一些具体的管理方法上、在一些质量工具应用过程中却存在着诸多的差别。例如德系企业的FMEA和美系企业的FMEA在做法就有所不同;日系企业的QFD到了欧美后就得到了简化和改良;美系企业的SPC和德系的SPC的也有很大的差别。各门各派武功不同,往往殊途同归。当然最关键的是,无论黑猫还是白猫,还是看你是否能抓到老鼠。
, z1 i+ e9 B% s- W0 D( H
因而在我看来,质量工具是活的东西。我也常常喜欢干些质量工具的创新和改良的活。目前我也有了很多这收获和心得,在一些企业中我已经把我的创新加以了运用,也得到了很好的反馈。
; x' c( k) Z, `$ e H- ?( }# |: k& F1 h
创新者的挑战
% z4 Y, ~. G4 u9 h; v1 E; P但也常常受到这样的挑战:“有哪家企业这样用过吗?”是不是也有这样的言外之意,只有被国外企业用过的东西才能算好东西,你玩创新你算老几?
只有被人用过的东西才算好东西,那么苹果手机刚上市的时候也不应该那么欢迎了。一个新鲜事物到底是不是好,有能力的人自信的人是需要自己来判定的。而跟随者的心态才是等到别人做了,再去见样学样。! M$ n6 j* Z2 V; ]. s( @
中国制造如果想超越,就一定要在产品技术上、工艺技术上、管理方法上、各质量工具应用上,要有在学习他人的基础上,完成自己的创新。在心态上要自信,要相信自己能够创新,也要接纳他人创新、鼓励创新。( _0 ^3 r5 R" h8 E
所有我还是希望大家要有开放的心态来学习、研究质量工具。质量工具是活的东西,千万不要用死了。( q4 d$ V5 g( ?& O1 U( J
我立志于建立一个中国人自己的、具有创新能力的质量管理咨询公司。这中间有很多艰辛,很多不理解,很多质疑,但同时也得到了很多的帮助,很多的肯定,和很多的鼓励。
作为一名草根创业者,我会一如既往的追求我的目标。因为我的梦已经融入了中国梦!中国制造将成为世人的骄傲,必将是我们这一代人的责任,责无旁贷!舍我其谁?
搞精益管理你必须要懂“5Why”
搞精益管理,需要知道五个为什么!所谓5why分析法,又称“5问法”,也就是对一个问题点连续以5个“为什么”来自问,以追究其根本原因。跟随来看精彩下文,希望对大家学习有助!
" z; H% b Y& G/ m5 w- a4 ?, @
5why法的关键所在
8 p+ C4 w. N# W8 I& \! k5 V1 g$ M5 v 鼓励解决问题的人要努力避开主观或自负的假设和逻辑陷阱,从结果着手,沿着因果关系链条,顺藤摸瓜,直至找出原有问题的根本原因。
; z+ L7 l. V L1 n2 v0 o5 t a
5Why的由来
* \" w) a& D1 b) _7 D m6 A0 o$ X, q
这种方法最初是由丰田佐吉提出的;后来,丰田汽车公司在发展完善其制造方法学的过程之中也采用了这一方法。作为丰田生产系统(Toyota Production System)的入门课程的组成部分,这种方法成为其中问题求解培训的一项关键内容。! ?& ^9 s! u( i# q% f6 }
* F& W4 K% D6 [5 R
丰田生产系统的设计师大野耐一曾经将五问法描述为:“……丰田科学方法的基础……重复五次,问题的本质及其解决办法随即显而易见。”目前,该方法在丰田之外已经得到了广泛采用,并且现在持续改善法(Kaizen),精益生产法(lean manufacturing)以及六西格玛法之中也得到了采用。
5Why经典小案例) V; u/ X0 c0 q. z7 o" \+ Q& }
* b5 o8 c$ P: V/ U. K
1. 停机的真正原因
* f2 v# e( F L0 \; E4 D
! G$ b- L4 ?5 j* l: y/ U
丰田汽车公司前副社长大野耐一曾举了一个例子来找出停机的真正原因:
$ |% ]. u! Y; o( v8 E7 {; n
★问题一:为什么机器停了?
答案一:因为机器超载,保险丝烧断了。
★问题二:为什么机器会超载?8 m% M: S N8 |% r$ P7 k* @
答案二:因为轴承的润滑不足。
★问题三:为什么轴承会润滑不足?
% R$ P% ?3 \7 n; U& I
答案三:因为润滑泵失灵了。
★问题四:为什么润滑泵会失灵?9 C/ Z2 A6 U7 h3 d2 I2 w
答案四:因为它的轮轴耗损了。
★问题五:为什么润滑泵的轮轴会耗损?# }; ~* g& q9 i5 e }1 h
答案五:因为杂质跑到里面去了。
! A. _' c+ `. ^2 c4 v 经过连续五次不停地问“为什么”,才找到问题的真正原因和解决的方法,在润滑泵上加装滤网。
& k8 }; L1 Y2 u8 _
如果员工没有以这种追根究底的精神来发掘问题,他们很可能只是换根保险丝草草了事,真正的问题还是没有解决。
8 e; w, z/ i1 a# b, r2.国会大厦的故事
! a4 v4 T% H( C7 t! u& K 据说美国华盛顿广场有名的杰弗逊纪念大厦,因年深日久,墙面出现裂纹。为能保护好这幢大厦,有关专家进行了专门研讨。
) |7 o4 J9 |% d: C
7 W& b% a' k1 y 最初大家认为损害建筑物表面的元凶是侵蚀的酸雨。专家们进一步研究,却发现对墙体侵蚀最直接的原因,是每天冲洗墙壁所含的清洁剂对建筑物有酸蚀作用。
% k0 K! i3 k) K, ` Q
★问题一:而每天为什么要冲洗墙壁呢?
答案一:是因为墙壁上每天都有大量的鸟粪。
3 m' _! S4 g. D6 Q★问题二:为什么会有那么多鸟粪呢?
答案二:因为大厦周围有很多燕子在住着。
! ^' w, R' s) w g
★问题三:为什么会有那么多燕子呢?
答案三:因为墙上有很多燕子爱吃的蜘蛛。
/ X! z3 v* R% m/ e# ^6 |
★问题四:为什么会有那么多蜘蛛呢?
答案四:因为大厦四周有蜘蛛喜欢吃的飞虫。
: [4 r6 J: H0 E* b" w★问题五:为什么有这么多飞虫?
答案五:因为飞虫在这里繁殖特别快。
+ Y+ |8 w5 u) X u9 S6 y
★问题六:为什么飞虫在这里繁殖特别快?
答案六:是这里的尘埃最适宜飞虫繁殖。
6 m% X! r) F4 X1 e' U: Y★问题七:为什么这里最适宜飞虫繁殖?
答案七:因为开着的窗阳光充足,大量飞虫聚集在此,超常繁殖……
& D# k7 \4 b9 i" ~9 B3 c) N' P
由此发现解决的办法很简单,只要关上整幢大厦的窗帘。此前专家们设计的一套套复杂而又详尽的维护方案也就成了一纸空文。彼得圣吉在《第五项修炼》里提到,问题的解决方案既有“根本解”,也有“症状解”,“症状解”能迅速消除问题的症状,但只有暂时的作用,而且往往有加深问题的副作用,使问题更难得到根本解决。“根本解”是根本的解决方式,只有通过系统思考,看到问题的整体,才能发现“根本解”。 我们处理问题,若能透过重重迷雾,系统思考,追本溯源,总揽整体,抓住事物的根源,往往能够收到四两拨千斤的功效。
0 x8 [- l3 q# Y
5Why的实施方法
* j& |+ L! w% u' Z4 ] t F, l A
5WHY从三个层面来实施:
: P; g: u% r2 |! L1 ^+ S/ N
0 [) T& @ J; H0 u @0 H一、为什么会发生?从“制造”的角度。
二、为什么没有发现?从“检验”的角度。
三、为什么没有从系统上预防事故?从“体系”或“流程”的角度。
每个层面连续5次或N次的询问,得出最终结论。只有以上三个层面的问题都探寻出来,才能发现根本问题,并寻求解决。
; `) {% @: M, d9 @4 r5Why分析法解决问题的基本步骤
{+ y- f' w4 a+ _; G) M4 {第一部分:把握现状
7 V9 M( Z @2 Q/ L4 L" K" N★步骤1:识别问题
在方法的第一步中,你开始了解一个可能大、模糊或复杂的问题。你掌握一些信息,但一定没有掌握详细事实。
, v3 C; L/ A3 ]/ ^★步骤2:澄清问题
方法中接下来的步骤是澄清问题。为得到更清楚的理解。
★步骤3:分解问题
在这一步,如果必要,需要向相关人员调查,将问题分解为小的、独立的元素。
★步骤4:查找原因要点(PoC)
★步骤5:把握问题的倾向
要把握问题的倾向,问:
谁?
哪个?
什么时间?
多少频次?
多大量?
在问为什么之前,问这些问题是很重要的。
: x' f M+ K7 j/ o1 M# L& f
第二部分: 原因调查
9 v, _+ i" O. K. z# L( E- K T★步骤6:识别并确认异常现象的直接原因。
如果原因是可见的,验证它。如果原因是不可见的,考虑潜在原因并核实最可能的原因。依据事实确认直接原因。
★步骤7:使用“5个为什么”调查方法来建立一个通向根本原因的原因/效果关系链。
★步骤8:采取明确的措施来处理问题。
/ [# E# C2 p, G! v
来源:网络